IDAH is the total solution provider for food, feed, and biofuel production
IDAH offers a complete selection of machines and parts for worldwide customers
IDAH Company today is the world's number one shrimp feed machine solution provider; we manufacture patented ContaTwin extruder, industry best sold pellet mill, dryer with patented Uniform Moisture Control, and have become the leader in texturized vegetable protein (TVP). We provide one-stop service which includes: R&D Prototyping, Education, Consultancy, Turnkey solution, Single Machine, and Spare Parts that helped our customers always stay one step ahead in the market.
With over 40 years of experience, we have enabled our customers to rapidly grow with our processing machines and complete turnkey project solutions in aquafeed, pet food, animal feed, extruded snack, textured vegetable protein (TVP), high moisture meat analogues (HMMA), plant-based meat, and wood pellets.
At IDAH, we understand that innovation grows from collective wisdom and experience. IDAH Innovation Center, an extrusion research lab, fosters an environment of innovation through open experiment by providing direct hands-on access to industry experts and machinery. We are committed to provide built-to-last machinery while also supporting our customers by providing robust OEM brand spare parts.
If you are in the feed, food, and biofuel industries. Come and visit us at IDAH, we will develop your next innovative products and have them realized.
The top 10 leading feed companies in Asia all rely on IDAH’s innovative technologies. Join them by entrusting IDAH as your machine and solution provider.
Product
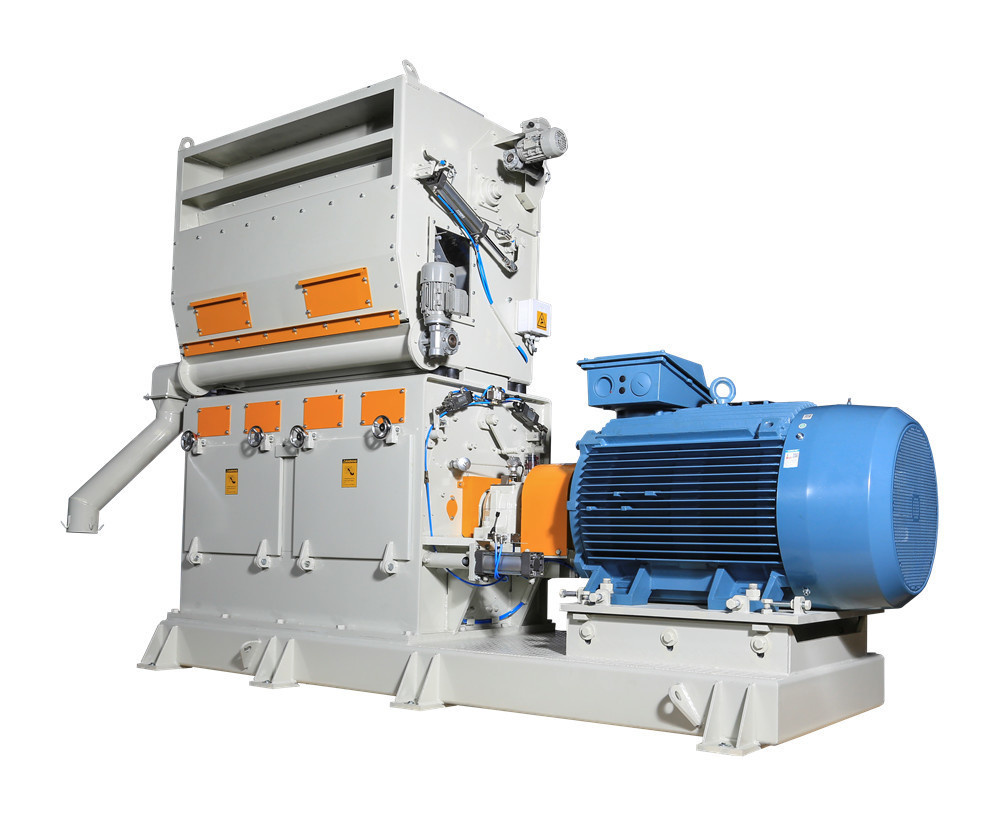
Grinding,Pulverizing, Crumbling
Grinding,Pulverizing, Crumbling
We provide different machines for particle reduction of various ingredients.
VIEW

Extrusion and Expander
Extrusion and Expander
Durable extruder for the production of high-quality product.
VIEW

Drying and Cooling
Drying and Cooling
Uniform and precise moisture control in the drying process.
VIEW

Pelleting
Pelleting
Designed for long-lasting performance with easy operation and low maintenance.
VIEW
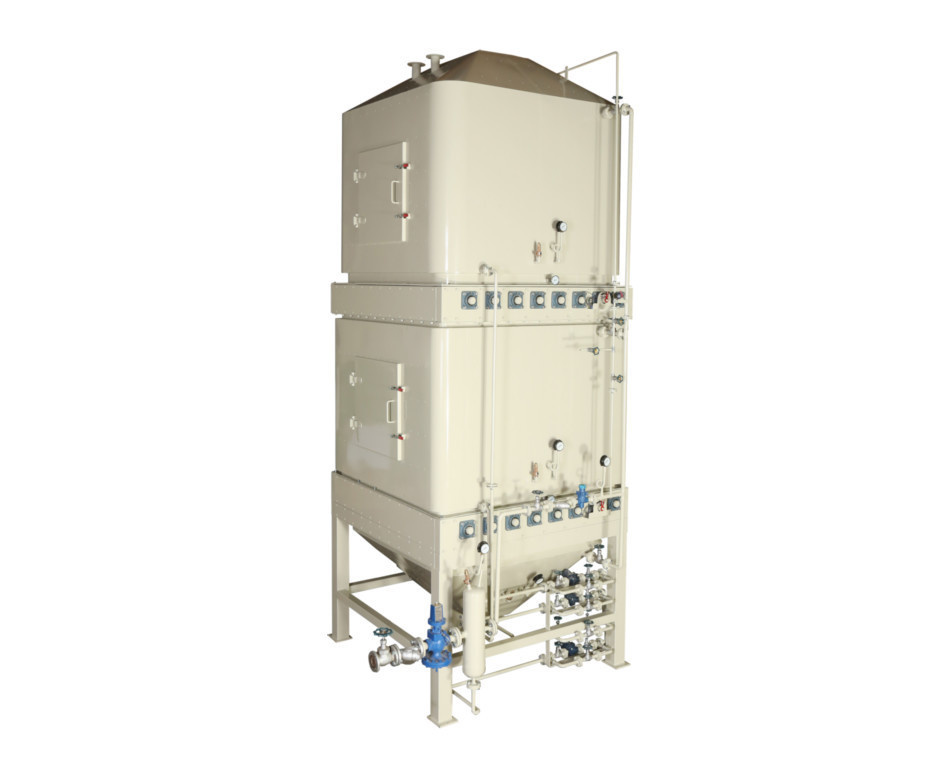
Conditioning
Conditioning
High efficiency material conditioner for extrusion and pelleting industry.
VIEW

Parts
Parts
Our spare parts are manufactured for OEM brands with design for assembly principles.
VIEW
Service
IDAH provides one-stop service which includes: R&D Prototyping, Education, Consultancy, Turnkey solution, Single Machine, and Spare Parts that helped our customers always stay one step ahead in the market.
Turnkey Projects
IDAH has completed over 300 turnkey projects in 21 countries since 1974. We have enabled our customers to rapidly grow by using our processing machines and complete plant solutions. These customers included the top 10 leading feed companies in Asia.
IDAH applied a 3D design program to simulate the process flow, to reduce the time and money needed while manufacturing machines, constructing machine towers, and machines installation.
IDAH Innovation Center
At IDAH, we understand that innovation grows from collective wisdom and experience. IDAH’s Innovation Center, an extrusion research lab, fosters an environment of innovation through open experimentation: providing direct hands-on access to industry experts and machinery. We can develop the competitive and innovative product with you.
READ MORE Technical Support
IDAH offers technical support for every step of your production process. Our consultancy includes plant management, formulation, quality control, and operator training. The scheduled onsite or online service is available for our customers. IDAH actively organizing technical seminars and training courses to share the latest technology and new ideas for process solutions.
READ MORE Maintenance
IDAH has 5 offices plus 10 plus agent worldwide. Technical supports can be provided on-time when question or problem is occurred. Please call us or contact us via internet, our experienced engineers will work with you to solve the problem, or our nearest engineer can visit the site to offer onsite consultation or technical supervision.
READ MORE Spare Parts
High quality spare parts is essential to maintain equipment at its prime performance. IDAH understands customers have strong demands for wear parts that attain on-time delivery and supreme quality. IDAH takes relentless efforts to develop new material systems for all wear parts for longer life span and installs modern production systems to support on-time delivery. All the efforts will in result to give customers minimized downtime and product costs.
READ MORE Solution
Aqua Feed
Our aquafeed solution produces sinking, slow-sinking, and floating feed. We design and manufacture reliable pelleting and extrusion systems for producing premium quality feed. The robust machinery with excellent configuration and high energy efficiency guaranteed to fulfill your production requirement.
Animal Feed
With over 40 years of accumulative experience, IDAH understands the importance of top-notch pre-conditioning configuration, pellet mill design, and operator-friendly control systems for producing high-quality animal feed. Our solution includes the production of cattle feed, pig feed, and poultry feed.
Pet Food
IDAH pet food solution produces dry kibbles and semi-moist pet food. Our pet food production featuring the patented ContraTwin extruder and the Carousel dryers with high uniformity drying performance. The solution guaranteed to produce high palatability and safe pet food for dogs, cats, rabbits, aquarium fish, and other specialized pet food.
Food
IDAH established the laboratory for food research and development in 1997. Our robust co-rotating twin-screw extruder supports the production of textured vegetable protein and snacks. With hands-on experience in making formulation, operating the machines, and marketing of food products, we are your ideal partner for your food industry.
Wood & Biomass
IDAH provides the integrated machinery and solution for processing wood and biomass material. Wood pellet and biomass pellets are one alternative of the sustainable source for combustion energy. The specially designed roller and pellet dies can provide high compression energy to press the material and generate high calorific value products.
Premix & Concentrates
Premix is an essential part of feed production. The combination of the vitamins and minerals in the premix will support the growth of the animals. IDAH micro-dosing and weighing scale systems can help premix or feed manufacturers to do the precise dosing and weighing of precious materials. The compact design guaranteed easy integration to your production line.
News Room
Successful Story
Want to know more? Let us know, we can help.
If you have any question, please don't hesitate to call us at +886-3-990-2701 or email us at [email protected]
Contact Us